Featuring high performance and small size, MEMS microphones are especially suitable for consumer electronics such as tablets, laptops, and smartphones. However, the microphone hole of these products is usually hidden inside the product, so the device manufacturer must design a sound path between the outside world and the microphone in order to transmit the sound signal to the MEMS microphone diaphragm. The design of this sound path has a significant impact on the overall performance of the system.
Below is a typical tablet microphone sound path:
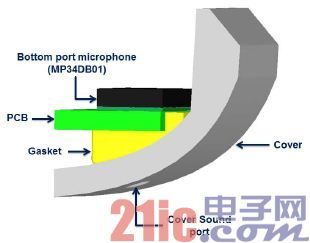
Figure 1 - Typical application examples
The sound path between the outside world and the microphone diaphragm is composed of the product housing, acoustic sealing ring, printed circuit board and microphone. This sound path acts as a waveguide to build the overall frequency response of the system. In addition, the acoustic impedance of the sound path material also affects the frequency response. To accurately predict the performance of the acoustic design, it is necessary to build a sound path model and use professional simulation tools such as COMSOL to simulate the frequency response characteristics of the sound path. However, this article provides readers with some basic principles for optimizing the sound path of a microphone.
Helmholtz resonance
The structure composed of narrow acoustic holes connected with hollow chambers will produce acoustic resonance when stimulated by sound waves. This resonance occurs when we blow air above the mouth of an empty bottle. The structure is called the Helmholtz resonator, named after Hermann von Helmholtz, the inventor of the phenomenon. Helmholtz uses resonators with different resonant frequencies to identify the frequency components of complex sounds such as music.
The center frequency of the Helmholtz resonance is determined by the following program:
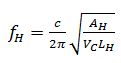
Where c is the air speed; AH is the cross-sectional area of the sound hole; LH is the length of the sound hole; VC is the volume of the cavity. The equation assumes that the resonator is a simple structure consisting of a cavity connected to a pipe of equal cross section. If the cross-sectional area and material of the sound path of the microphone are different, the equation describing the acoustic characteristics of the sound path is much more complex. Therefore, it is necessary to simulate the acoustic characteristics of the whole sound path to accurately predict the overall performance of the acoustic design.
In this paper, by changing the thickness and inner diameter of the microphone seal ring, the diameter of the sound hole of the product housing, the diameter of the sound hole of the printed circuit board, the bending of the sound path and the acoustic impedance of the path material, we carry out the frequency response simulation experiments on different sound paths. The experimental results allow designers to predict in advance the extent to which changes in these parameters will affect the overall performance of the sound path.
The frequency response of the microphone
The low frequency of the MEMS microphone is determined by the following main parameters: the size of the ventilation hole between the front and back of the sensor diaphragm; Volume of the posterior chamber. The high frequency of MEMS microphones is determined by the Helmholtz resonance generated by the sound hole in the front chamber of the microphone.
For most MEMS microphones, when the sensitivity of the microphone drops to low frequency and then rises to high frequency, the frequency response curve is roughly the same because of the Helmholtz resonance. However, different MEMS mics differ greatly in sensor design, package size and structure, so the overall frequency response, especially the high frequency response, varies greatly. Most of ST's microphones place the sensor directly above the sound hole to minimize front chamber volume and ensure excellent high frequency response.
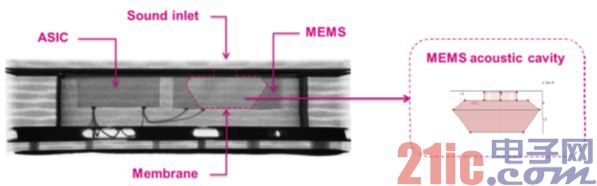
Figure 2 - X-ray image of the ST MP34DT01 upper sound hole microphone and its sound chamber
The following simulation results describe the frequency response of the ST MP34DB01 MEMS microphone itself. The simulation tool solves the equation at each discrete point of the sound path model, and at the end of the simulation, plots the data collected at all useful points.
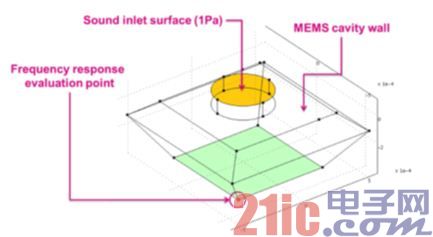
Figure 3 - Sound chamber for MP34DB01 and MP34DT01 MEMS microphones
The MP34DB01 microphone simulation results show that the frequency response curve is very flat in the high frequency part, and at 20 kHz, the typical sensitivity increase is about +3dB, which is due to the high center frequency of the Helmholtz resonance. The simulation results are very close to the actual measured frequency response of MP34DB01.
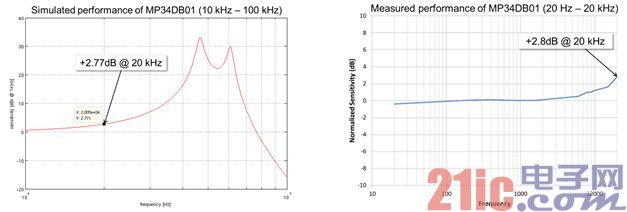
Figure 4 - MP34DB01 MEMS microphone frequency response simulation results and actual measurement results
Effect of sealing ring thickness on frequency response
The microphone sealing ring plays an airtight role between the microphone sound hole and the product housing sound hole. After a microphone seal is installed, the length from the sound hole to the microphone front chamber is extended, resulting in a change in frequency response. In the following simulation experiment, round tubes of different lengths but with a fixed diameter (400μm) are placed on the microphone hole to evaluate the extent to which the sealing thickness affects the frequency response.
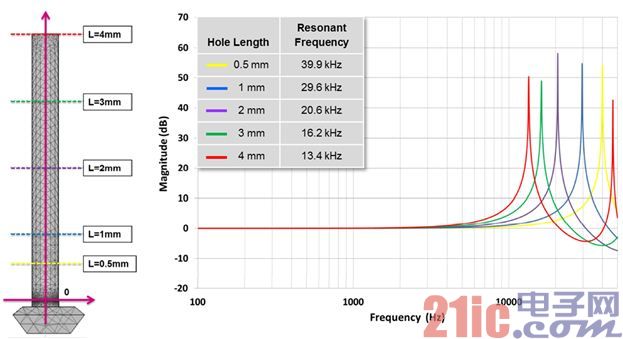
Figure 5 - Relation between MP34DT01 frequency response and seal thickness
It is not difficult to see from the simulation experiment that adding a sealing ring will destroy the frequency response performance. After the sealing ring is added (if it is a lower sound hole microphone, it is also added a printed circuit board), the actual sound hole length is extended, resulting in a lower resonant frequency and an increased sensitivity of the high frequency part. A thicker seal will increase the length of the resonator bottleneck, resulting in a lower resonant frequency and poorer high-frequency response performance.
Effect of inner diameter of sealing ring on frequency response
The next simulation experiment was to evaluate the effect of seals with different inner diameters but fixed thickness (2mm) on frequency response. FIG. 6 shows the simulation results of seals with different inner diameters.
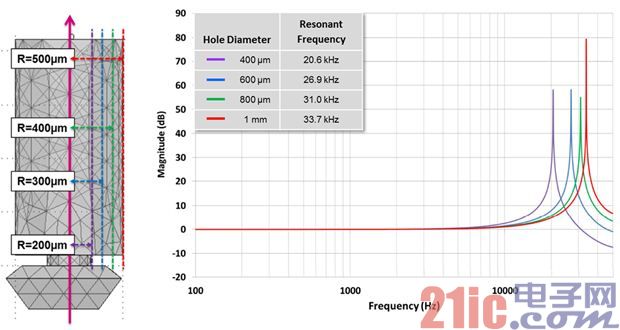
Figure 6 - Relation between MP34DT01 frequency response and inner diameter of sealing ring
These simulation data show that increasing the inner diameter of the microphone sealing ring can increase the resonant frequency and improve the overall frequency response performance.
The influence of sound path shape on frequency response
So far, the simulation results are consistent with the predicted results obtained by solving the Helmholtz resonance equation. The following simulation experiment discusses the influence of sound path shape changes on frequency response, which is difficult to predict. The structure shown in Figure 7(a) is a simple sound path with a length of 4mm and a diameter of 600μm, and other simulation experiments are based on this simple structure. In order to simulate changes in the width and shape of sealing rings, product housing sound holes and printed circuit board sound holes, the simulation experiment adds different lengths, radii and shapes of the cavity, and the sound path becomes very complicated.
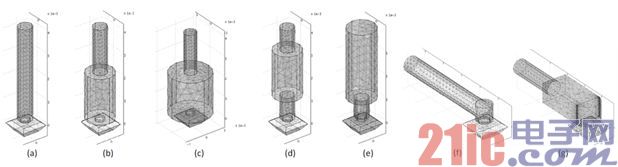
图 7 – 声音路径形状变化
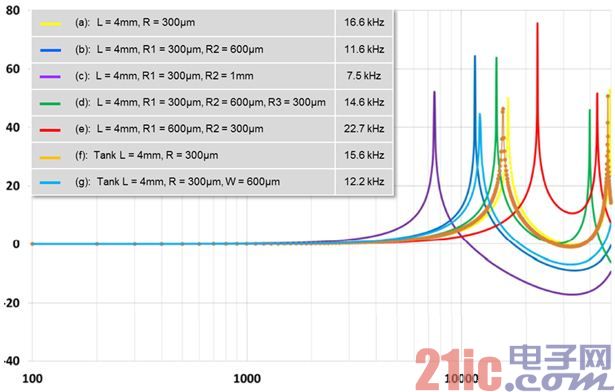
Figure 8 - Frequency response of MP34DB01 at different sound path shapes
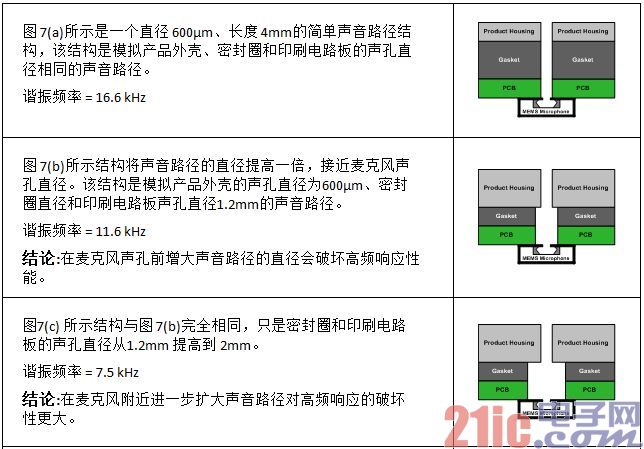
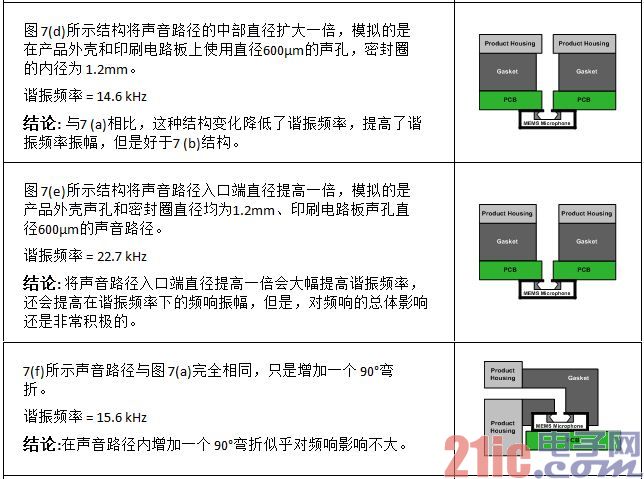
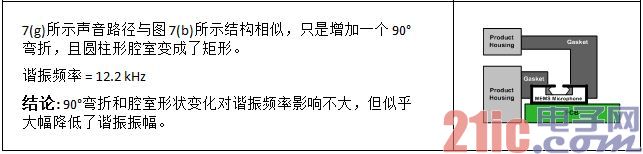
The effect of sealing ring material on frequency response
All the simulation experiments so far have focused on the influence of sound path shape on frequency response, and applied sound hard boundary conditions to all path surfaces. The following simulation experiment discusses the effect of sealing ring acoustic impedance on frequency response. As shown in Figure 9, this experiment applies suitable acoustic impedance to the surface of the acoustic hole (yellow), sensor cavity (powder) and sensor diaphragm (green), while the acoustic impedance of the blue surface is variable. The acoustic impedance of a material is the product of the density of the material and the speed of sound passing through the material (Z = ρ·c). Seals are usually made of rubber or other elastic materials, while typical product housing materials are usually plastic, aluminum or steel.
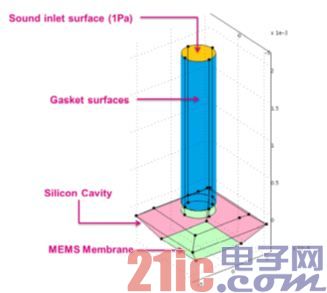
图 9 – 声音路径表面
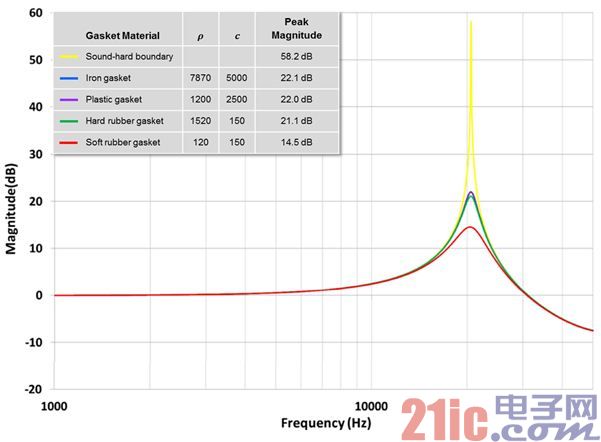
Figure 10 - Effect of seal material on resonance peak amplitude
Because the resonant frequency is determined by the shape of the sound path, although changing the acoustic impedance of the sealing ring will not affect the resonant frequency, it will affect the resonant Q value. Although the sound path maintains continuous resonance, the softer seal reduces the resonance and reduces its effect near the resonant frequency. Compared with the experimental results using hard boundary conditions of sound, the sound hole with iron surface material significantly reduces the peak frequency response amplitude, which indicates that the severity of the test results using hard boundary conditions of sound is unrealistic.
Case study - Analyze the entire sound path of the sound hole mike under the tablet
Figure 11 shows the sound path of a tablet's lower sound hole mike. In this example, the lower sound hole is mounted on a printed circuit board, and an airtight soft rubber seal is inserted between the printed circuit board and the product housing.
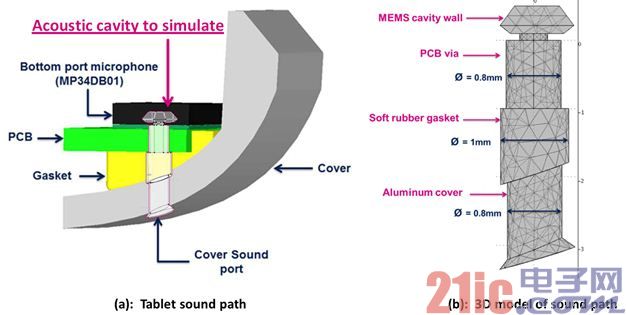
Figure 11 - The sound path design and 3D model of the sound cavity for the tablet MAC
In this simulation experiment, all components of the sound path are set up with appropriate acoustic characteristics. Figure 11(b) shows a 3D model of the sound path of structure 11(a). All materials used in this simulation are commonly used in consumer electronics: FR4 printed circuit boards, soft rubber seals, and aluminum bodies.
Figure 12 - Simulation results of tablet MAC sound path
FIG. 12(a) shows the frequency response curve of a sound path with a resonant peak frequency of about 21.6 kHz, and FIG. 12(b) shows the distribution of air pressure in the sound path at a resonant frequency of 21.6 kHz. At this resonant frequency, the MEMS diaphragm is subjected to the greatest pressure.
Conclusion The following guidelines help to optimize the frequency response of the microphone sound path.
● The shortest and widest sound path possible. Widening the external entrance of the sound path helps improve the frequency response, while widening the microphone end of the sound path reduces the frequency response performance.
● Try not to have any cavities in the sound path. If you can't avoid it, try to keep the cavity away from the mike hole.
● Sound path curvature seems to have little effect on frequency response.
● Soft sealing ring material can weaken resonance and improve frequency response performance.
免责声明: 本文章转自其它平台,并不代表本站观点及立场。若有侵权或异议,请联系我们删除。谢谢! Disclaimer: This article is reproduced from other platforms and does not represent the views or positions of this website. If there is any infringement or objection, please contact us to delete it. thank you! 矽源特科技ChipSourceTek |