People often take it for granted to power the circuit of the PCB, not knowing that this can cause damage and damage or non-destructive latch conditions. These problems may not be prominent until the start of mass production, when the tolerance of the device and design is tested, but it is too late, the project and product time and delivery will be greatly affected, and the cost will be greatly increased. To address the errors found during this phase, a number of modifications will be required, including PCB layout changes, design changes, and additional anomalies.
With the advent of the integrated circuit era, many functional modules are integrated into one IC, so it is necessary to use multiple power supplies to power these modules. The voltages of these sources are sometimes the same, but more often they are different. The increasing number of system-on-chip (SoC) ics on the market has created a need for sequential control and management of power supplies.
Analog Devices' data books usually provide enough information to guide design engineers in designing the correct power-on sequence for each IC. However, some ics explicitly require that an appropriate power-on sequence be defined. This is true for many of Analog Devices' ics. This requirement is common in ics that use multiple power supplies, such as converters (including ADC and DAC), digital signal processors (DSPS), audio/video, RF, and many other mixed-signal ics. Essentially, ics that contain some kind of analog input/output with a digital engine fall into this category and may require specific power timing control. These ics may have separate analog and digital power supplies, and some even have digital input/output power supplies, see the specific examples discussed below for details.
This application note discusses some of the more subtle power supply issues that design engineers must consider in a new design, especially when the IC requires multiple different power supplies. At present, some of the more commonly used power supply voltages are: +1.8V, +2.0V, +2.5V, +3.3V, +5V, +12V, and −12V.
PULSAR ADC example - Absolute maximum rating
All Analog Devices data books contain an Absolute Maximum Rating (AMR) section, which describes the maximum voltage, current, or temperature that can be applied to the pin or device to avoid causing damage.
The AD7654PulSAR 16-bit ADC is an example of a mixed-signal ADC with three (or more) independent power supplies. These ADCs require a digital power supply (DVDD), analog power supply (AVDD), and digital input/output power supply (OVDD). They are ADCs that convert analog signals into digital code, so an analog core is required to process the incoming analog input. The digital kernel handles the bit determination process and control logic. The I/O kernel is used to set the level of the digital output for interface with the host logic (level conversion). The power supply specifications for the ADC can be found in the "Absolute Maximum Rating" section of the corresponding data sheet. Table 1 is taken from the "Absolute Maximum Ratings" section of the AD7654 (Rev.B) data book.
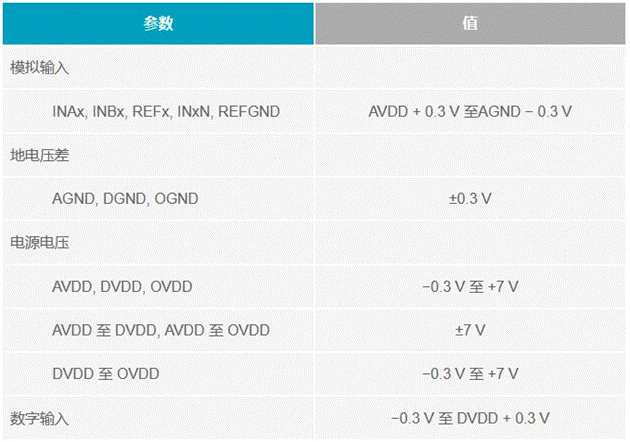
Table 1. Absolute Maximum rating of the AD7654 (Rev.B)
Note that all three power supplies in Table 1 range from −0.3V to +7V. Compared to DVDD and OVDD, AVDD ranges from +7V to −7V, which confirms that either AVDD or DVDD is powered on first. In addition, either AVDD or OVDD is powered on first. However, there are limitations between DVDD and OVDD. The technical specifications stipulate that OVDD can only be up to 0.3V higher than DVDD, so DVDD must be powered on before or at the same time as OVDD. If OVDD is powered on first (assuming 5V), then DVDD is 5V lower than OVDD when powered on, which does not meet the "absolute maximum rating" requirement and may damage the device. The limitation of analog inputs INAx, INBx, REFx, INxN, and REFGND is that these inputs must not exceed AVDD +0.3V or AGND −0.3V. This means that if the analog signal or reference voltage source is present before the AVDD, the analog core is likely to be powered up to a latched state. This is usually a lossless condition, but the current flowing through the AVDD can easily gradually rise to 10 times the nominal current, causing the ADC to become quite hot. In this case, the internal electrostatic discharge (ESD) diode becomes positively biased, which powers up the analog power supply. To address this issue, the input and/or reference voltage source should be unpowered or disconnected when the ADC is powered on.
Similarly, the digital input voltage ranges from −0.3V to DVDD +0.3V. This means that the digital input must be less than DVDD +0.3V. Therefore, when powering on, the DVDD must be powered on before or at the same time as the microprocessor/logic interface circuit. Similar to the analog core situation described above, ESD diodes on these pins can also become positively biased, powering the digital core to an unknown state.
PulSAR ADCs such as the AD7621, AD7622, AD7623, AD7641, and AD7643 are newer to the family and use a lower 2.5V power supply (the AD7654 uses a 5V power supply). The AD7621 and AD7623 have a well-defined power-on sequence. Table 2 is taken from the "Absolute Maximum Ratings" section of the AD7621 (Rev.0) data book.
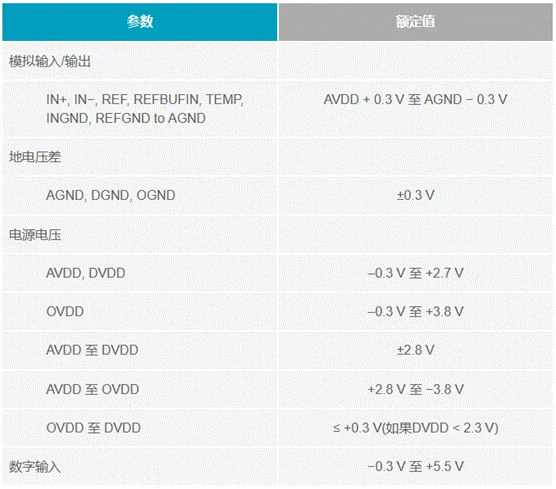
Table 2. Absolute maximum rating of the AD7621 (Rev.0)
Again, there are limitations between OVDD and DVDD. The "absolute maximum rating" stipulates that OVDD must be less than or equal to DVDD+0.3V, while DVDD must be less than 2.3V. Once the DVDD reaches 2.3V during power-on, this limit no longer applies. If this limitation is not followed, the AD7621(and AD7623) may be compromised (see Figure 1).
Figure 1. Possible power-on/shutdown sequence - AD7621 (Rev.0)
Therefore, the general power-on sequence may be as follows: AVDD, DVDD, OVDD, VREF. However, each application is different and requires specific analysis. Note that device shutdown is as important as device power-on, and remember to follow the same specifications. Figure 1 shows a typical power-on/shutdown sequence for the AD7621. For these ADCs, the analog input and reference voltage source are the same as described above. Applying a voltage to any analog input pin can cause the ESD diode to become positively biased, thus powering the analog core to an unknown state. The digital input and output of these ADCs are slightly different, as these devices should support 5 V digital inputs. These ADCs are speed-upgraded versions of the AD7654, and both the digital input and output are associated with the OVDD power supply, as it can support a higher 3.3V voltage. Note: Digital input is limited to 5.5V, while the AD7654 is DVDD+0.3V.Example of type Σ-Δ ADC
AD7794 type Σ-Δ 24-bit ADC is another good example. Table 3 is taken from the "Absolute Maximum Ratings" section of the AD7794 (Rev.D) data book.
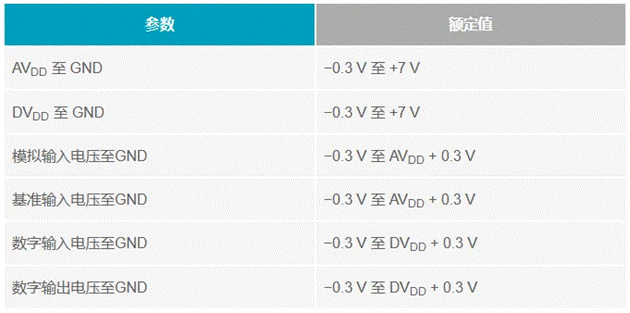
Table 3. Absolute Maximum rating of the AD7794 (Rev.D)
The problem with this ADC is related to the reference voltage, which must be less than AVDD + 0.3V. Therefore, AVDD must be powered on before or at the same time as the reference voltage.Power sequential controller Analog Devices offers a number of power sequential control devices. In general, the working principle is that when the output voltage of the first regulator reaches a preset threshold, a time delay is initiated, and subsequent regulators are powered on only after the delay is over. The procedure during a shutdown is similar. A timing controller can also be used to control the timing of logical signals such as power supply good signals, for example by applying a reset signal to a device or microprocessor, or simply indicating that all power supplies are active.Suggestion Today, most circuit PCBS that require high speed and low power consumption require multiple power supplies, such as +1.8V, +2.0V, +2.5V, +3.3V, +5V, +12V, and −12V. Powering these power supplies on a PCB is no easy task. Careful analysis is required to design a correct and reliable power-on and shutdown sequence. The use of discrete design is becoming more and more difficult, the solution is to use the power timing control IC, as long as a change in the code can change the power-on sequence, without changing the PCB layout.
免责声明: 本文章转自其它平台,并不代表本站观点及立场。若有侵权或异议,请联系我们删除。谢谢! Disclaimer: This article is reproduced from other platforms and does not represent the views or positions of this website. If there is any infringement or objection, please contact us to delete it. thank you! 矽源特科技ChipSourceTek |