Source: ON Mei Author: On Mei
Motor drive systems (EMDS) are highly dependent on position encoders to increase efficiency and meet increasingly stringent regulatory requirements. As shown in Figure 1, the position encoder feeds the perceived speed and position information back to the controller, enabling high-precision motor control and synchronization. There are many types of position encoders, including mechanical, optical, magnetic or inductive.
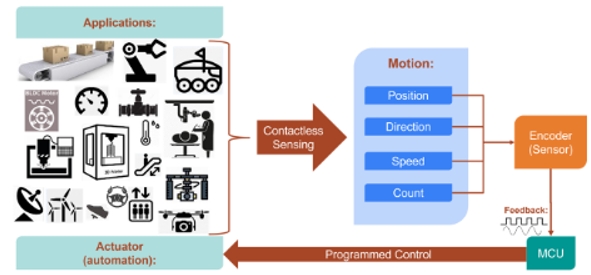
Figure 1: High precision motor control and synchronization via encoder
It is worth noting that rotary inductor encoders have significant advantages in harsh environments and can effectively resist the influence of pollution factors such as dirt, magnetic debris, moisture and shock. Based on the Faraday electromagnetic induction principle, these devices are widely used in various fields of Industry 4.0, and can measure the position movement of many industrial systems such as transmissions, pedals, and robotic arms.Principle of rotating inductance sensor A typical rotary inductance encoder has three main components, as shown in Figure 2. The rotor is mounted on the rotating motor shaft and the stator is mounted on the encoder housing. Both the rotor and stator have flat coils that are integrated onto the PCB, while position-sensing devices such as onsemi's NCS32100 inductive position sensor are typically mounted on the stator. The sensing device transmits the sine wave (4 MHz for the NCS32100) to an exciting coil on the stator, which acts as an antenna, coupling the energy to the receiving coil of the rotor. The stator also has a set of receiving coils, and when the rotor rotates, the coupling energy in the coils will disturb the stator receiving coils. The sensing device is connected to the stator receiving coil to receive the input signal and measure the rotor position by analyzing the disturbance in the stator receiving coil. By increasing the number of rotor and stator coils, changing the mode of the coils, and increasing the number of inputs received by the sensing device, the resolution and accuracy of the rotary inductor encoder can be improved.
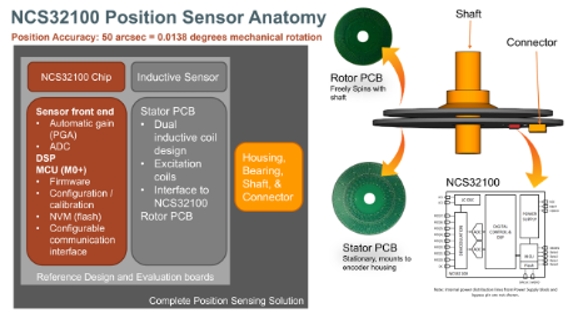
Figure 2: A rotary inductance encoder has three main components
On Mei NCS32100 introduction The NCS32100 is a newly patented dual inductance sensor that is ideal for industrial market applications including robotics, motor control and positioning, servo applications, and more. The NCS32100 supports static high-speed applications, achieving accuracy of 50 arcseconds or more at speeds up to 6,000 rpm, with functional rotor speeds up to 45,000 rpm. The full-featured controller and sensor interface, when used with a non-contact PCB sensor, enables high-resolution, high-precision Angle perception. The device features a highly configurable 8-channel sensor interface that supports the connection of many types of inductive sensors and offers a rich digital output format. In addition, it provides speed, temperature and backup battery measurements, and an integrated power circuit supports a wide VCC range and backup battery capability.On's Web-based design tool The overall resolution and accuracy of the rotary inductor encoder depends on the design of the stator and rotor PCB and the performance of the sensing device. PCB design is challenging, with strict tolerance requirements for parameters such as line width and spacing, through hole pad diameter, drill hole diameter, copper and insulation thickness. Given that improper design can greatly affect the performance of encoders, ON has created the Web-based NCS32100 PCB design tool to guide engineers through the necessary PCB design steps. When using the tool, the user follows a three-step process (see Figure 3) : First enter a clear set of data to describe the encoder design, then generate a detailed drawing of the rotor and stator PCB, and finally run a simulation based on the input design parameters. These simulations run by the user simulate receiver input amplitude and angular error (arcseconds) based on input parameters, and by iterating these parameters, the solution can be optimized for cost and accuracy requirements.
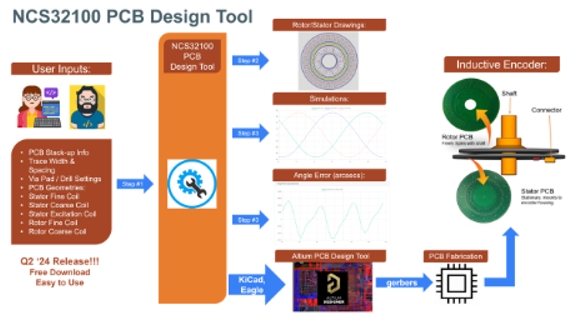
Figure 3: A three-step development process using the NCS32100 PCB design tool
On Beauty helps you reach profitability faster Rotary inductor encoders are a common choice for motor control solutions in harsh industrial environments because of their robustness and resistance to contamination. While On's NCS32100 sensor offers designers a highly accurate and configurable solution, a poor PCB design can degrade the overall performance of any encoder system that uses the sensor. The NCS32100 PCB design tool gives designers the confidence to optimize their PCB designs without having to invest resources in prototyping. PCB coil design tools support rapid iteration of a range of input options to help designers quickly optimize PCB designs based on cost and accuracy requirements, speeding up the development process and reducing time to market. Industrial system manufacturers are confident in the accuracy of their NCS32100-based designs, as in tests conducted by On Semiconductor, the level of accuracy of the device is comparable to the precision Gurley encoder, which is considered an industry benchmark.
免责声明: 本文章转自其它平台,并不代表本站观点及立场。若有侵权或异议,请联系我们删除。谢谢! Disclaimer: This article is reproduced from other platforms and does not represent the views or positions of this website. If there is any infringement or objection, please contact us to delete it. thank you! 矽源特科技ChipSourceTek |